Application: | Drinking Water Supply | Standard: | ISO4427/EN12201, DIN8074/8075 |
---|---|---|---|
Material: | 100% Virgin Material PE100 &PE80 | Specification: | DN20mm-1600mm |
Product Name: | High Density Polyethylene HDPE Pipe Polypipe For Drinking Water Supply | Pipe Color: | Black With Blue Stripe |
PE100 | 0.4MPa | 0.5MPa | 0.6MPa | 0.8MPa | 1.0MPa | 1.25MPa | 1.6MPa | 2.0MPa | 2.5MPa |
Outside Diameter | PN4 | PN5 | PN6 | PN8 | PN10 | PN12.5 | PN16 | PN20 | PN25 |
SDR41 | SDR33 | SDR26 | SDR21 | SDR17 | SDR13.6 | SDR11 | SDR9 | SDR7.4 | |
Wall Thickness (en) | |||||||||
20 | - | - | - | - | - | - | 2.0 | 2.3 | 3.0 |
25 | - | - | - | - | - | 2.0 | 2.3 | 3.0 | 3.5 |
32 | - | - | - | - | 2.0 | 2.4 | 3.0 | 3.6 | 4.4 |
40 | - | - | - | 2.0 | 2.4 | 3.0 | 3.7 | 4.5 | 5.5 |
50 | - | - | 2.0 | 2.4 | 3.0 | 3.7 | 4.6 | 5.6 | 6.9 |
63 | - | - | 2.5 | 3.0 | 3.8 | 4.7 | 5.8 | 7.1 | 8.6 |
75 | - | - | 2.9 | 3.6 | 4.5 | 5.6 | 6.8 | 8.4 | 10.3 |
90 | - | - | 3.5 | 4.3 | 5.4 | 6.7 | 8.2 | 10.1 | 12.3 |
110 | - | - | 4.2 | 5.3 | 6.6 | 8.1 | 10.0 | 12.3 | 15.1 |
125 | - | - | 4.8 | 6.0 | 7.4 | 9.2 | 11.4 | 14.0 | 17.1 |
140 | - | - | 5.4 | 6.7 | 8.3 | 10.3 | 12.7 | 15.7 | 19.2 |
160 | - | - | 6.2 | 7.7 | 9.5 | 11.8 | 14.6 | 17.9 | 21.9 |
180 | - | - | 6.9 | 8.6 | 10.7 | 13.3 | 16.4 | 20.1 | 24.6 |
200 | - | - | 7.7 | 9.6 | 11.9 | 14.7 | 18.2 | 22.4 | 27.4 |
225 | - | - | 8.6 | 10.8 | 13.4 | 16.6 | 20.5 | 25.2 | 30.8 |
250 | - | - | 9.6 | 11.9 | 14.8 | 18.4 | 22.7 | 27.9 | 34.2 |
280 | - | - | 10.7 | 13.4 | 16.6 | 20.6 | 25.4 | 31.3 | 38.3 |
315 | 7.7 | 9.7 | 12.1 | 15.0 | 18.7 | 23.2 | 28.6 | 35.2 | 43.1 |
355 | 8.7 | 10.9 | 13.6 | 16.9 | 21.1 | 26.1 | 32.2 | 39.7 | 48.5 |
400 | 9.8 | 12.3 | 15.3 | 19.1 | 23.7 | 29.4 | 36.3 | 44.7 | 54.7 |
450 | 11.0 | 13.8 | 17.2 | 21.5 | 26.7 | 33.1 | 40.9 | 50.3 | 61.5 |
500 | 12.3 | 15.3 | 19.1 | 23.9 | 29.7 | 36.8 | 45.4 | 55.8 | - |
560 | 13.7 | 17.2 | 21.4 | 26.7 | 33.2 | 41.2 | 50.8 | 62.5 | - |
630 | 15.4 | 19.3 | 24.1 | 30.0 | 37.4 | 46.3 | 57.2 | 70.3 | - |
710 | 17.4 | 21.8 | 27.2 | 33.9 | 42.1 | 52.2 | 64.5 | 79.3 | - |
800 | 19.6 | 24.5 | 30.6 | 38.1 | 47.4 | 58.8 | 72.6 | 89.3 | - |
900 | 22.0 | 27.6 | 34.4 | 42.9 | 53.3 | 66.2 | 81.7 | - | - |
1000 | 24.5 | 30.6 | 38.2 | 47.7 | 59.3 | 72.5 | 90.2 | - | - |
1200 | 29.4 | 36.7 | 45.9 | 57.2 | 67.9 | 88.2 | - | - | - |
1400 | 34.3 | 42.9 | 53.5 | 66.7 | 82.4 | 102.9 | - | - | - |
1600 | 39.2 | 49.0 | 61.2 | 76.2 | 94.1 | 117.6 | - | - | - |
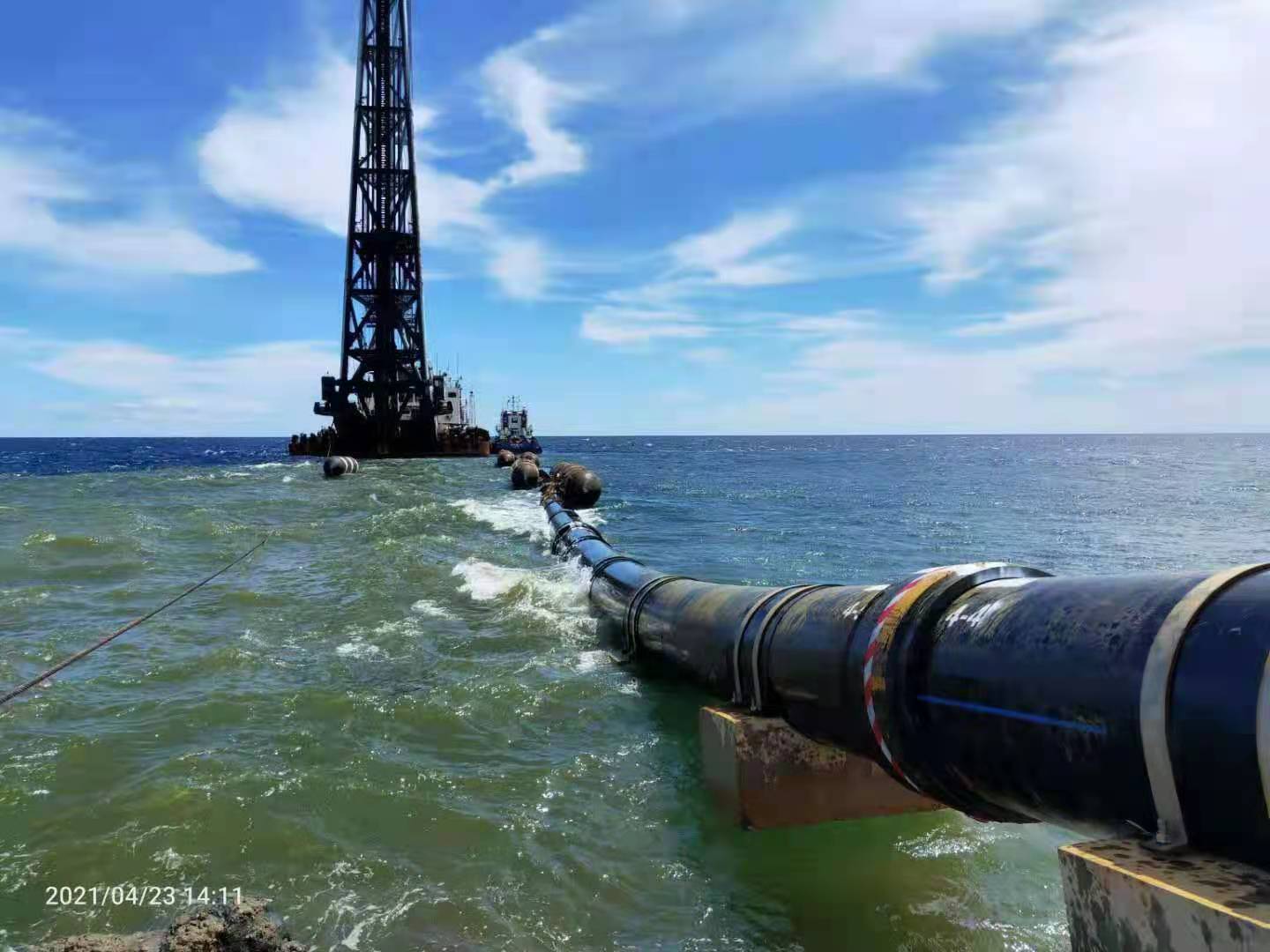
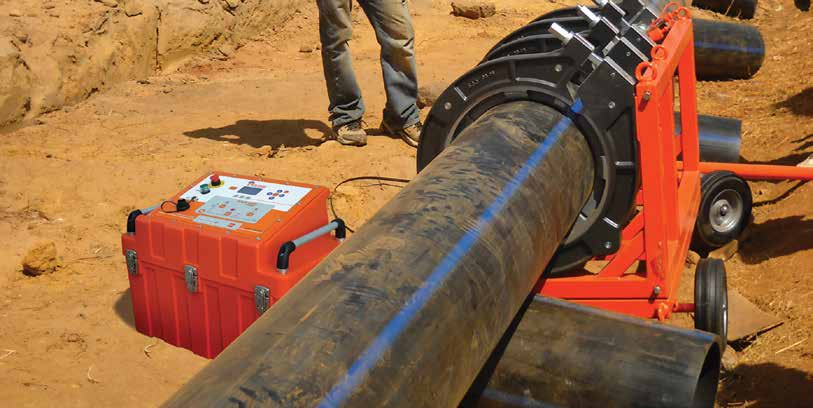
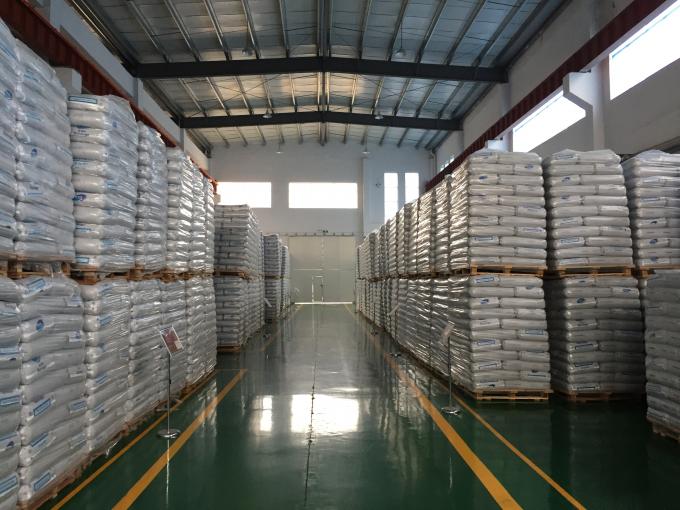
SI NO. | PROPERTIES | UNIT | REQUIREMENT | Experimental parameters | Experimental Method |
1 | Density | Kg/m³ | More than 930(base resin) | 190℃,5KG | D method of GB/T1033-1986,experimental preparation is according to GB/T1845.1-1989 : 3.3.1 |
2 | Melt Flow Rate (MFR) | g/10min | 0.2-1.4,and the maximum deviation should not exceed the nominal value of the mix | 190℃,5kg | GB/T3682-2000 |
3 | Thermal stability (oxidation induction time) | min | More than 20 | 200℃ | GB/T17391-1998 |
4 | Volatile content | Mg/kg | Less than 350 | Appendix C | |
5 | Moisture content b | Mg/kg | Less than 300 | ASTMD4019:1994a | |
6 | Carbon black content c | % | 2.0-2.5 | GB/T13021-1991 | |
7 | Carbon black dispersion c | grade | Less than 3 | GB/T18251-2000 | |
8 | Pigment dispersion d | grade | Less than 3 | GB/T18251-2000 | |
9 | Resistant to gas components | h | More than 20 | 80℃,2Mpa(ring stress) | Appendix D |
Bear fast crack propagation (RCP) | |||||
10 | Full size (FS) experiment :Dn ≥250mmor S4 experiment:pipe wall thickness ≥15mm | MpaMpa | Full size experiment’s critical pressure Pc.fs ≥ 1.5XMOP | 0℃0℃ | ISO13478:1997GB/T19280-2003 |
11 | Bear slow crack propagation (En≥5mm) | h | 165 | 8℃,0.8Mpa(experiment pressure) f 80℃,0.92Mpa(experiment pressure) g | GB/T18476-2001 |
a Non-black blends should meet the weatherability requirements in Table 6 b Water content is measured when the measured volatiles do not meet the requirements. When arbitration, the water content should be the measurement results as a basis for judging c Only apply to black mixd Only apply to non-black mix e If the S4 test results do not meet the requirements, you can follow the full-size experiment to re-experiment to full-size experimental results as the final basis. f PE80, SDR11 experimental parameters g PE100, SDR11 experimental parameters |
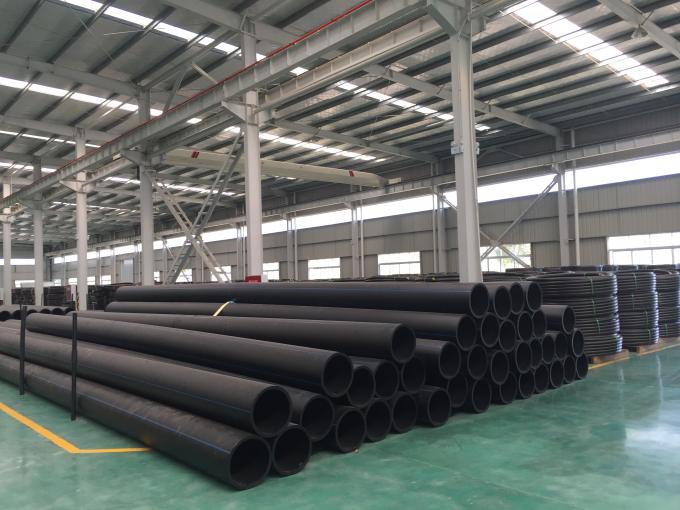
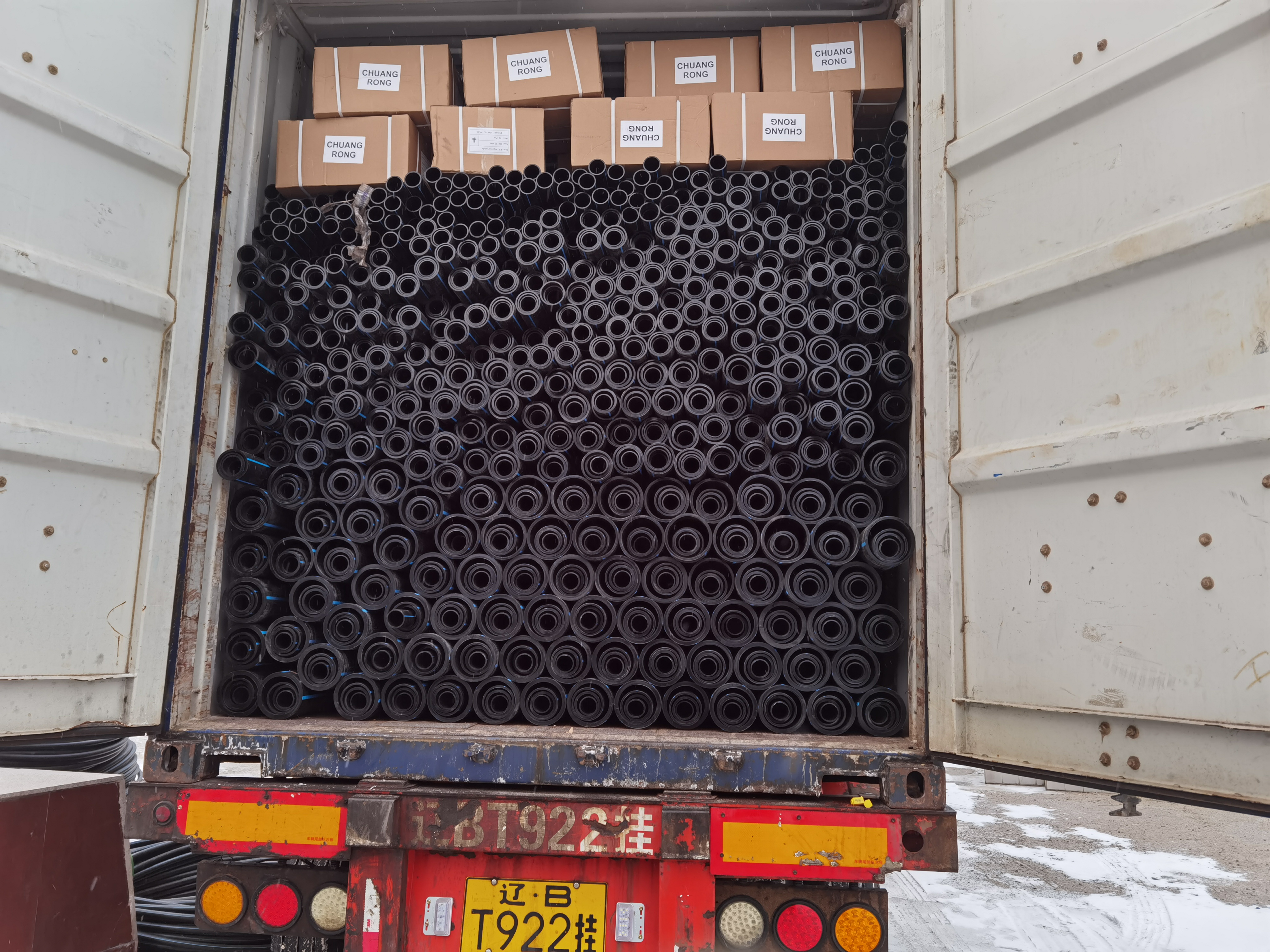
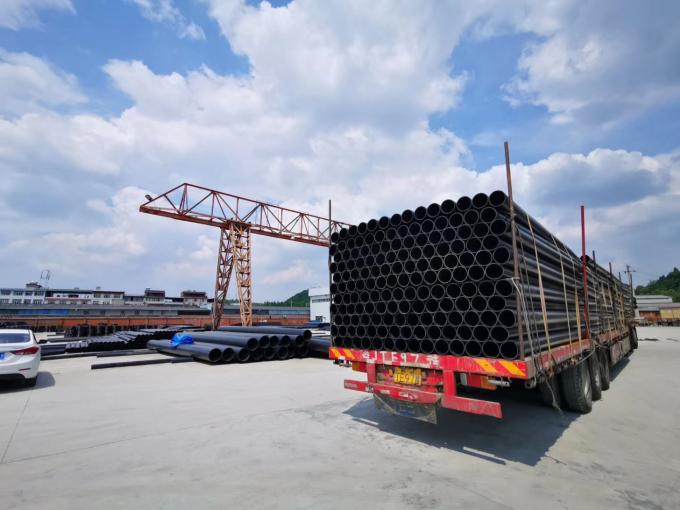
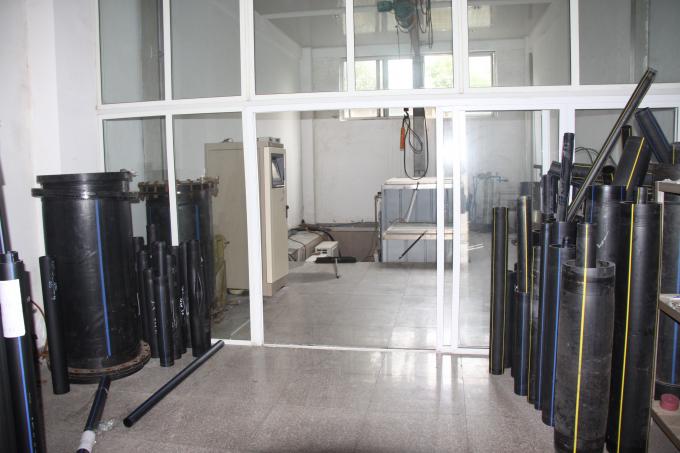
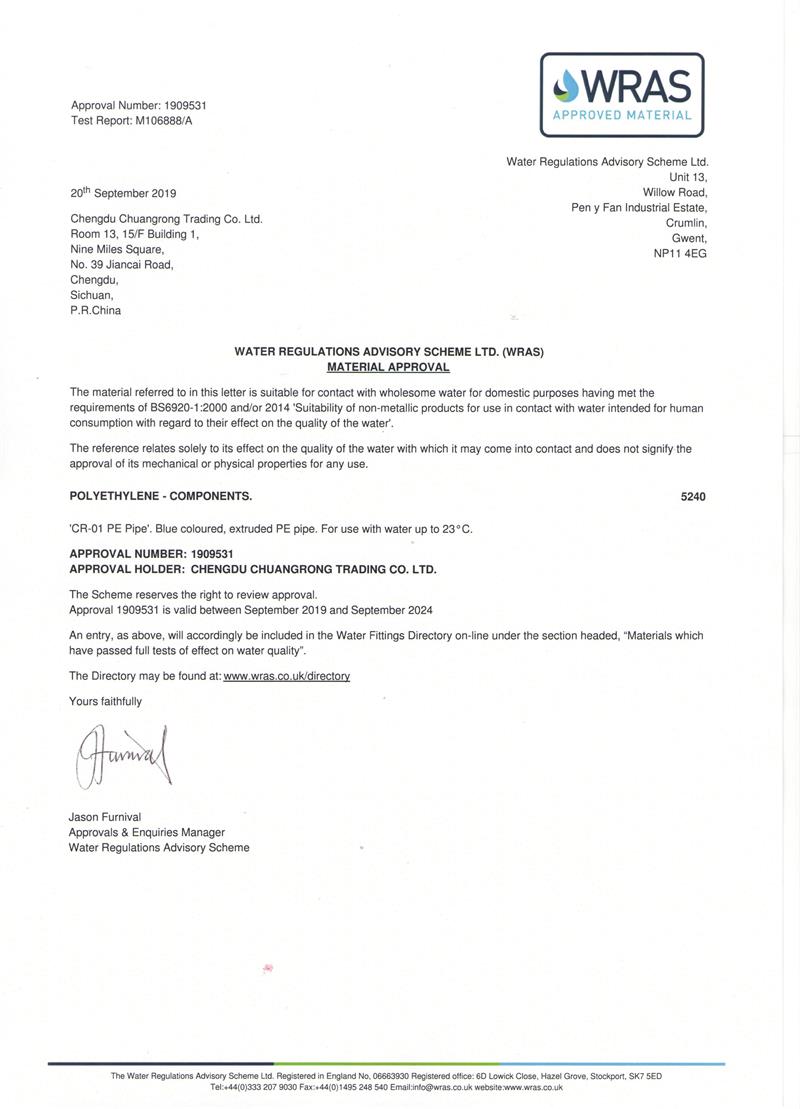
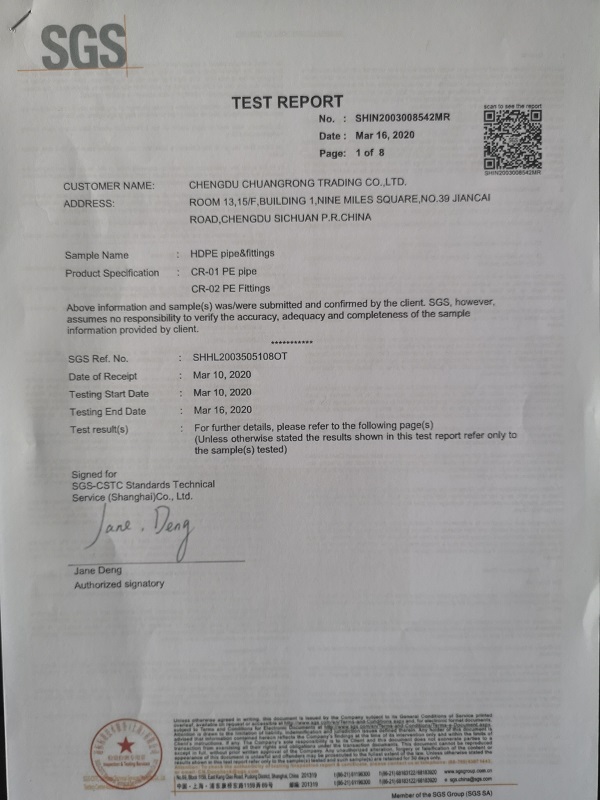
No | Items | HDPE Pipe |
1 | Molecular | ≥300 000 |
2 | Density | 0.960 g/cm3 |
3 | Tensile breaking strength | ≥28 Mpa |
4 | Longitudinal contraction rate of return | ≤3% |
5 | Breaking elongation | ≥500% |
6 | Resistant to corrosion | good |
7 | Tensile strength | ≥28Mpa |
8 | Static hydraulic strength | 1)20℃,cycle stress 12.4Mpa,100h,no break,no leakage |
2)80℃,cycle stress5.5Mpa,165h,no break,no leakage | ||
3)80℃,cycle stress5.0Mpa,1000h,no break,no leakage | ||
9 | MFR(190℃,5kg,)g/10min | ≤25% |
10 | Oxidation induction time (200℃)min | ≥20 |
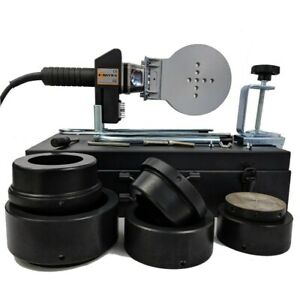
Butt Fusion Joint
1.Securely fasten the components to be joined
2.Face the pipe ends
3.Align the pipe profile
4.Melt the pipe interfaces
5.Join the two profiles together
6.Hold under pressure
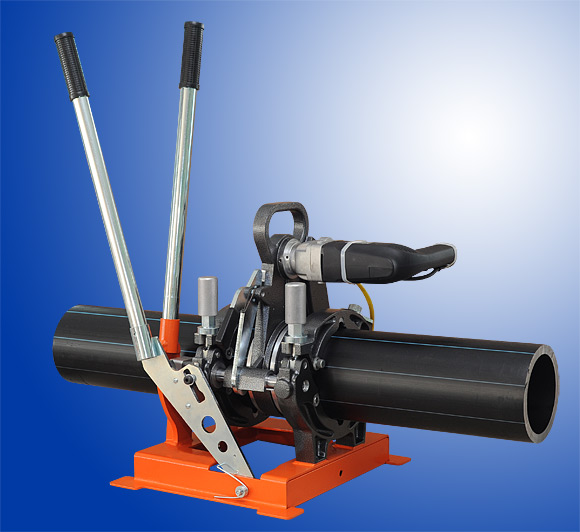
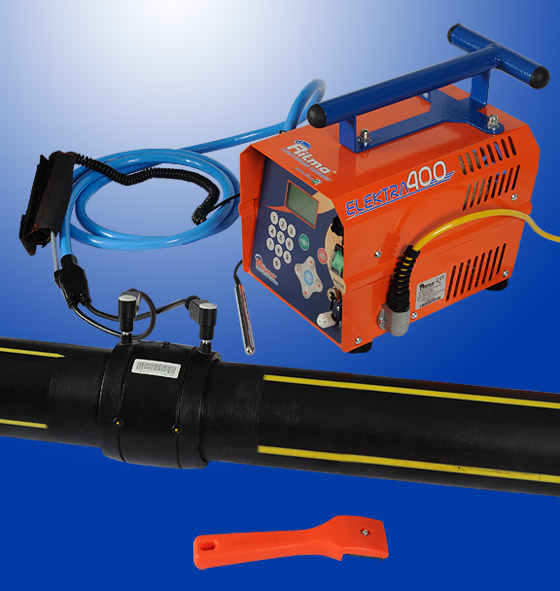
Electro Fusion Joint
1.Prepare the pipes
2.Clamp the fittings and pipe(s)
3.Apply the electric current
4.Cold and remove the clamps
Compression Fittings Joint
A Chamfer the pipe with beveler tool
B Slackend the ring nut with out removing from the body check that O-ring and clip ring are in proper position.
C Insert the pipe end with out tightening the ring nut.Push the fitting until the pipe oversteps the O-ring and reaches the stop
D Hand tighten the ring unt the tighten further with a strap/chain wrench.
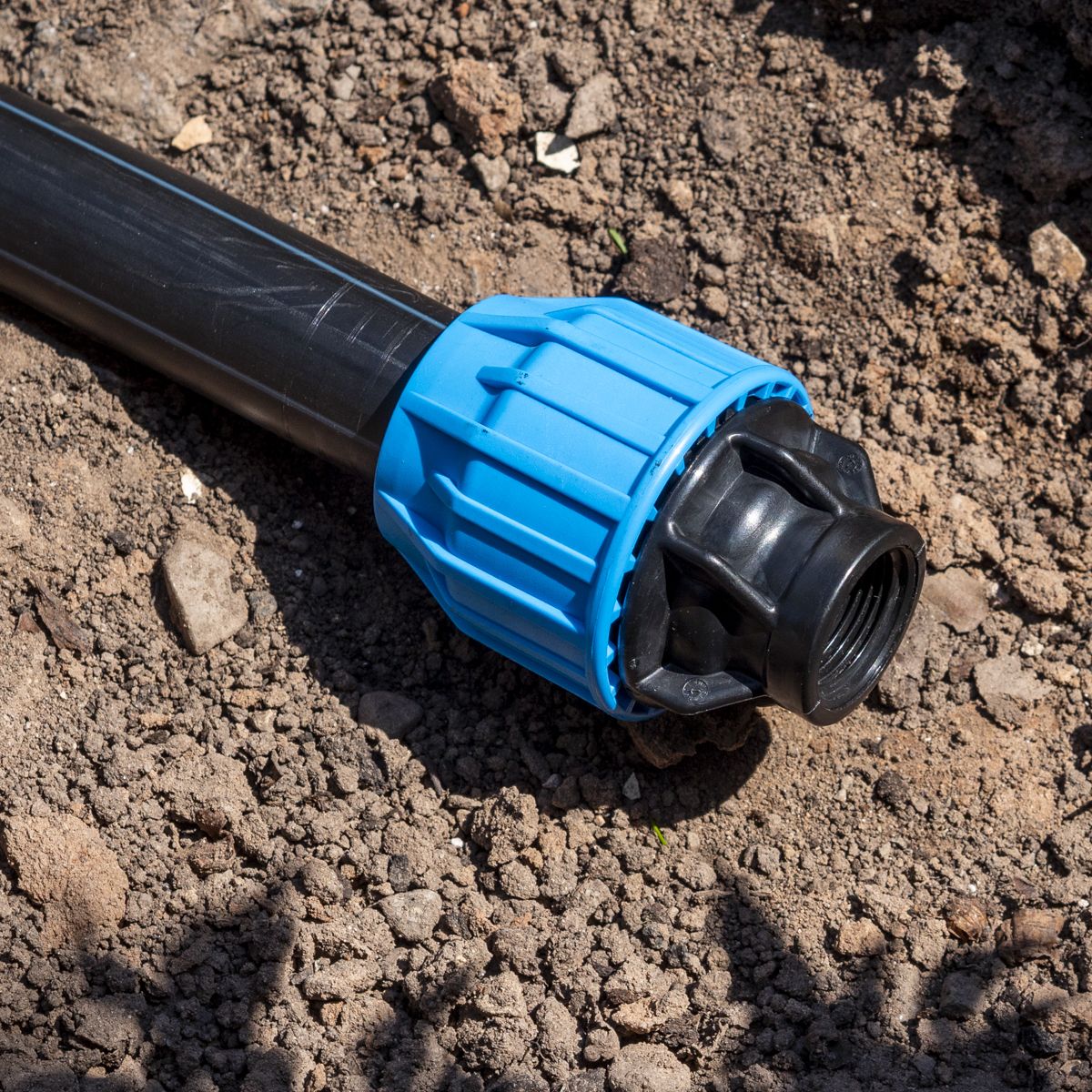
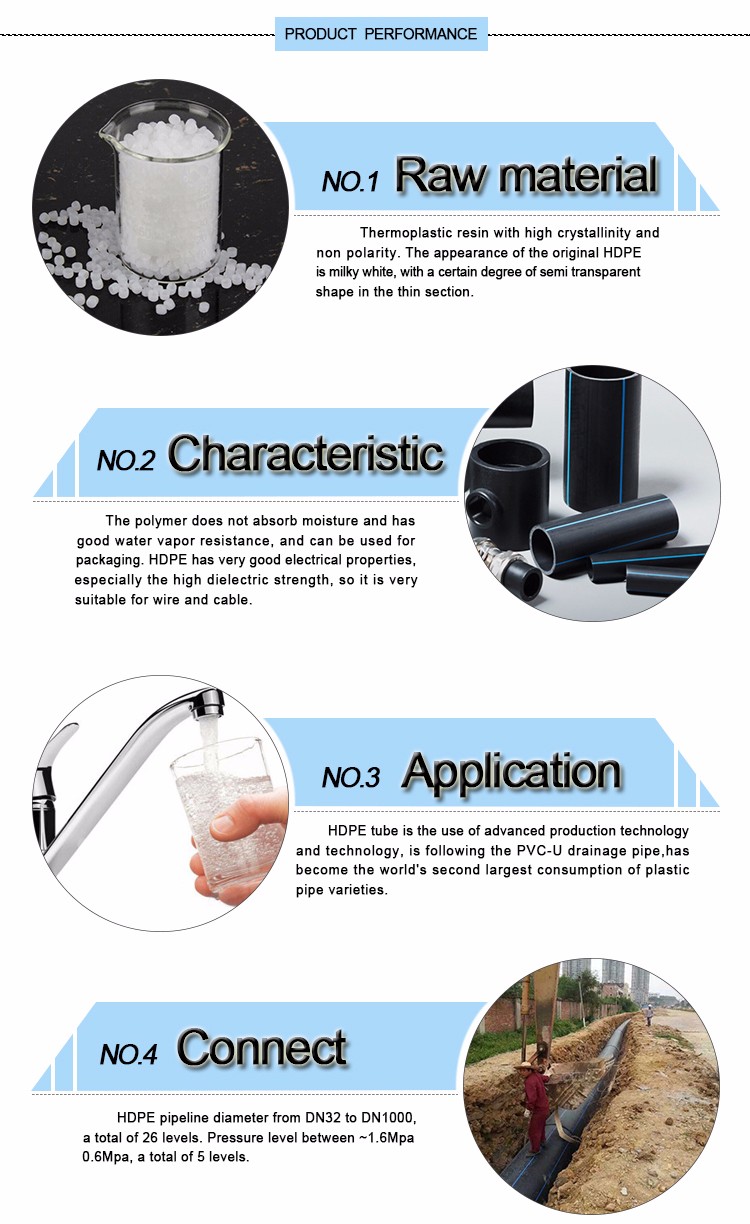
Socket Fusion Joint
1.Select the equipment
2.Square and prepare the pipe ends
3.Heat the parts
4.Join the parts
5.Allow to cool.
No. | Item | Requirements | |
1 | Percentage of breaking-elongation,% | ≥350 | |
2 | Longitudinal reversion(110℃),% | ≤3 | |
3 | Oxidation induction time (200℃)min | ≥20 | |
4 | Weather resistance 1. (After the pipe has accepted the aging energy which equal to or more than 3.5GJ/m2) | 80℃ static hydraulic strength (165h) | No break, no leakage. |
Percentage of breaking-elongation,% | ≥350 | ||
Oxidation induction time (200℃)min | ≥10 | ||